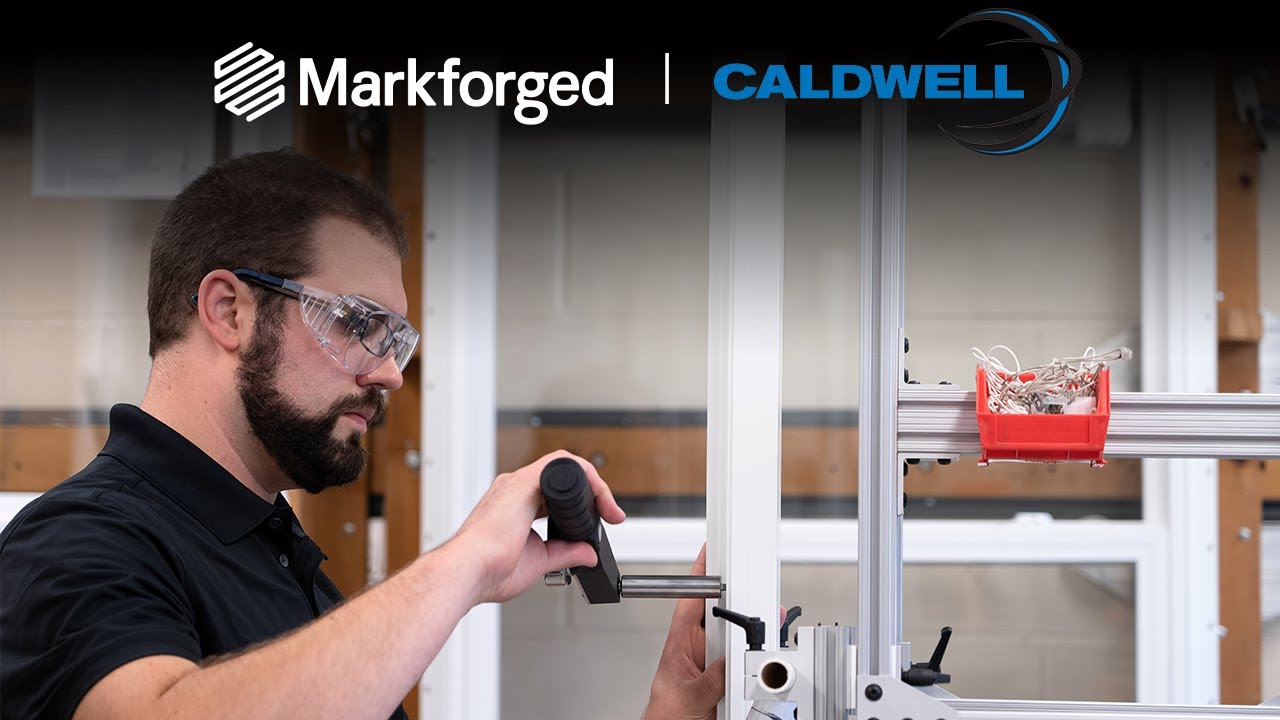
US-based Caldwell Manufacturing ships window and door components to businesses in over 70 countries. The company’s hardware can be found in residential homes, medical buildings, schools, and even the Empire State Building in New York City. These parts need to be tested before the final part is made, and the rigorous tests check whether they will stand up against hurricanes and other natural events. The team used traditional manufacturing methods and third parties to make their R&D parts, as well as in-house tooling for their factory floor, but found it was too expensive and time consuming.
Caldwell Manufacturing turned to Markforged 3D printers to speed up their R&D process, as well as the fabrication of non-revenue-generating tools. “We selected Markforged based on our level of confidence with them,” says Rick de Normand, Product Engineering Manager at Caldwell Manufacturing. They purchased a Markforged Metal X and several Markforged carbon fiber printers.
Since purchasing the Markforged 3D printers, the team has created everything from 3D printed metal and carbon fiber window components for testing, all the way to carbon fiber reinforced robotic grippers and assembly fixtures.
“The Markforged Onyx material gives us another level of strength above what we could previously print with other FDM technologies. For test equipment, strength and rigidity is key,” says Matt Brady, Test Engineer at Caldwell Manufacturing.
Our Website:
Twitter:
Instagram:
Facebook:
LinkedIn:
0 Yorumlar